11 Strategies To Completely Block Your Pallet Prices
Roslyn
0
2
12.20 13:17
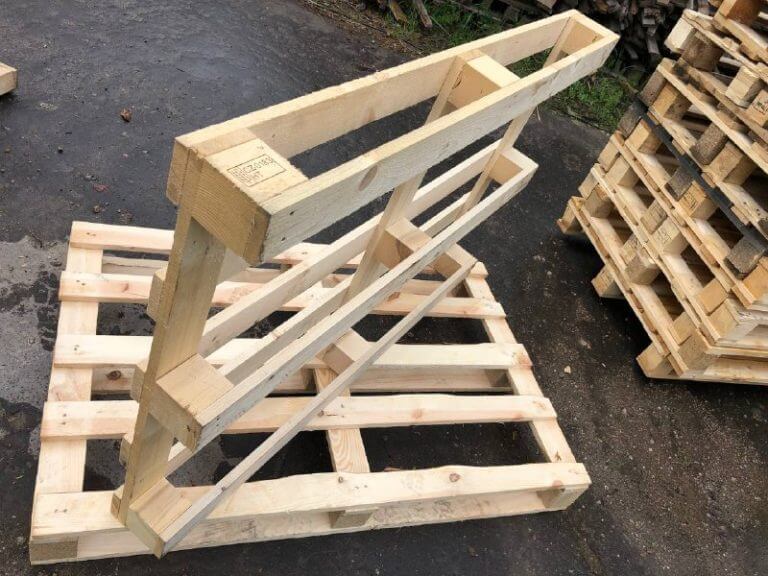
Many factors influence the price of a pallet, which includes its size and material. It is also based on market conditions and the availability of raw materials. It is essential to keep these factors in mind when you negotiate prices for pallets.

Cost of raw materials
Pallets appear to be simple products but they're much more than just wood and nails. For one, pallet manufacturers have to account for fixed overhead costs, which include machinery, rent insurance, utilities, and administrative salaries. These costs are more stable than labor or raw materials, but they can increase in the future due to inflation or changes in local economies. In addition, some manufacturers are forced to raise their prices due to the rising cost of costs for shipping and lumber.
The cost of pallets can differ greatly based on the quality and availability of lumber. Many pallet manufacturers make use of less-quality wood that is less expensive than the higher grade that are used for furniture or construction. The demand for these lower grade woods, however, has driven raw lumber prices up. This has led to an abrupt increase in the cost of the materials required to construct a pallet.
In the pallets made of purchase wood pallets, lumber is typically the most significant component of the overall cost. Since it is a commodity, the price of wood can be extremely volatile, and this can have a major impact on the cost of pallets. Other components that could have an impact on the cost of a pallet include fasteners, labor, and overhead costs.
Pallet prices are also affected by demand and supply which can influence the price of both new and recycled wood pallets. In times of high demand, like around holidays or during harvest season, the cost of pallets can be higher than other times.
Another factor that affects the price of pallets is the cost of shipping. Costs for fuel, driver shortages and the distance of shipping can all impact the cost of pallets. Shipping costs can be high for companies that depend on pallets to transport their products.
The size and type of material may also affect the cost. A plastic pallet, for example, might cost more than one made of wood due to the fact that it is generally thicker. A plastic pallet is more durable and can withstand more trips than a wood pallet. These advantages can make the additional cost worthwhile for certain businesses.
Cost of labor
When it is time to determine the price of High-Quality Factory-Made Pallets the cost of labor is an important element. This is particularly true when pallets are frequently used pallets for sale. In addition to the expense of raw materials, the manufacturer also has to consider other inputs like fasteners and labor. It is ultimately all these factors that determine the price a pallet costs. The price of raw materials is determined by market conditions and the price of labor is determined by local wage rates.
Prices for pallets are a complex combination of variables, which is difficult to predict. Raw material prices can fluctuate based on the demand and supply of lumber, and other materials like resin and core. In addition, the price of transportation is a major factor in the total cost.
In terms of raw materials, the most significant element in the cost of the new pallet of wood is the cost of lumber. Prices for lumber are rising due to a number of factors including logging restrictions and the influenza pandemic. The supply of lumber has been affected by the drought and forest fires that have spread across the country.
The type of wood used to build the pallet and the size of its deck are additional factors that can influence the cost. The majority of wood pallets are constructed of southern yellow pine (SYP), but other species are available as well. In general, softwoods are less expensive than hardwoods.
Another significant aspect of the cost of a pallet is type of fasteners used make it. Special or standard fasteners can be found in a variety of sizes. Standard fasteners can be more affordable, but require more manual labor. The length of time the pallet is kept in storage will also affect its cost. It can be either long-term or short-term storage and will depend on the demands of the seasons for your company.
Pallets have where to get pallets be transported to customers after they are built. Cost of fuel, distances to shipping and availability of drivers can all affect the cost of pallets. Additionally, some customers have specific delivery requirements that result in fewer than the truckload limit being shipped, which could increase the cost per pallet.
Cost of manufacturing
The cost of pallet manufacturing differs greatly based on the nature and quality of the materials used. Wood is among the most expensive raw materials used in the production of pallets. Additionally, labor costs are another major factor. Pallets require labor to cut and assemble the wood. These factors can result in significant price increases of pallets when compared to the raw material costs of lumber. Many supply chains have switched to metal or plastic pallets to reduce these costs.
It isn't easy to handle the erratic nature in pallet prices. This is especially relevant for businesses that rely heavily on pallets, including manufacturing, retail, and consumer electronics. Fortunately, there are ways to help businesses navigate these market turmoils. One of these steps is to look at how the company purchases its pallets. This will help reduce costs and improve efficiency.
In general, pallets are a key element of the supply chain and should be considered an essential part of any supply chain strategy. While the cost of pallets has risen significantly but it is expected to level out in the coming years. Warehouse automation companies are investing more to meet increasing demand for pallets.
Lumber prices have reached the bottom of the barrel and are gradually increasing. However, wild card events like weather conditions that hinder logging and uncertainty about the outcome of a CN rail strike in Canada could cause lumber prices to rise again.
Pallet manufacturers also have to take into consideration other aspects including transportation and logistics costs. These expenses are determined by the distance between the pallet maker and the buyer as well as how long it takes the pallets to arrive at the destination. The quantity of pallets you order will also impact the price because larger orders typically result in lower costs per pallet due to economies-of-scale.
There are a myriad of factors that affect the price of pallets, including the type and quality of the materials used as well as manufacturing processes and size specifications. There are pallets that are cheaper by using recycled materials or by altering the specifications. You can also opt to use plastic pallets, or even stainless steel pallets.
Transport costs
Shipping pallets provide a stable platform on which goods can be transported. They are a crucial tool for warehouse operations. A well-designed pallet can help reduce packaging costs and improve efficiency. However the cost of transportation can also be a significant factor in determining pallet prices. The cost of transportation is affected by a variety of factors, including the dimensions and type of pallets, the materials used, and the distance traveled.
The prices of pallets have slowed considerably in 2023 due to lower demand, lower lumber prices, and increased pallet core availability. However, pallet providers still have labor issues to overcome. Pallet buyers need to establish relationships with a pallet provider who is knowledgeable and experienced. This will allow them to design their pallet strategy for the months and years to come.
The availability of raw materials is the most important factor when determining pallet for sale prices. Lumber, the largest component of new pallets is currently at a five-year low. However, seasonal factors such as conditions that hinder the logging process and uncertainty over a CN rail strike in Canada could push lumber prices higher in the near future.
Other factors that affect pricing for pallets include the kind and size of the pallet, its condition and whether it is treated with heat for international shipment. For instance pallets made of wood are more expensive than wood stringer pallets due to the fact that they require a particular heat treatment process. Pallets that are smaller in quantity and with custom sizes are usually more expensive than standard High-Quality Factory-Made Pallets.
Another important aspect is the load-to-truck ratio, which is a critical measurement for freight transportation and can raise transport costs. This metric shows the amount of freight that is displayed on DAT load boards in relation to the truck capacity available. A high ratio could result in delays in securing transportation, which can impact the reliability of services and raise costs for shippers. A low ratio of load-to-truck can lower shipping costs and enhance services. The best goal for any freight shipper is to maintain an appropriate load-to-truck ratio.